Rolex is one of the most recognizable brands in the world, famed for creating extremely valuable, high-quality luxury watches. However, despite the iconic status of some of its timepieces and the company’s global popularity, it remains shrouded in secrecy, closely guarding many of its watch-making processes.
Indeed, the manufacturer makes a conscious effort to be as discreet as possible, even implementing a strict ‘no photography’ policy at its four main sites in Switzerland. Nevertheless, visitors to the sites have been able to observe the way the company operates, helping to build a clearer picture of the way Rolex makes its watches.
In this article, we take a closer look at the pioneering watchmaker and examine some of its manufacturing techniques.
Four Manufacturing Sites
With the exception of sapphire crystals and watch hands, every individual part of a Rolex watch – from the case, to the strap, to the mechanical movement – is manufactured on-site at one of four locations. All four locations can be found within Switzerland and activities are divided as follows:
BIENNE – The only one of the four sites based outside of Geneva, the Bienne facility is where Rolex movements are produced. Each movement is manufactured by hand, with the site’s skilled team often having to work with extremely small components. Assembly is carried out with such precision that all movements made at the facility meet the Swiss Official Chronometer Testing Institute (COSC)’s strict accuracy criteria.
PLAN-LES-OUATES – This location is where processes surrounding the watch cases and bracelets are performed. Activities here include the creation of the 18 ct gold alloys used on the company’s watches, the subsequent casting of that gold, and the final polishing of the individual parts, in order to get them ready for final assembly.
CHÊNE-BOURG – The Chêne-Bourg facility is where gem-based activities take place, from gemmology to the gem-setting processes. In addition, the manufacture of Rolex dials also takes place here.
ACACIAS – Serving as the company’s world headquarters, this building houses communication activities, design activities, sales services and research and development labs. The science labs are used for everything from testing the lubricants used on machinery to stress testing on the timepieces themselves, simulating wear and tear in order to ensure that the cases and internal components are robust and fit for purpose.
Materials
Since 2003, Rolex have updated steel-related activities, dealing only in 904L stainless steel. This is a type of steel which is more resistant to rust and corrosion than the 316L stainless steel used by almost all other watch manufacturers. It is also harder than other types of steel, helping it to withstand intense and repeated polishing.
In general, 904L steel is more visually impressive than other varieties, but is harder to work with, which is why most manufacturers opt for the standardised 316L variety instead. Rolex receives its steel from a small number of suppliers, but all steel is then worked in-house, using top-of-the-range machinery.
All gold and platinum is made in-house, with the company producing yellow gold, white gold and a non-fading 18 ct gold known as Everose gold. It would appear that Rolex is the only watch manufacturer in the world to have its own on-site foundry, providing the opportunity to melt gold and turn it into cases and other components.
Research and Testing
Rolex’s research and development department works around the clock to create new technology, more precise movements and truly innovative functions. More than 6,000 workers are employed by the company, with many of them being scientists and other researchers.
Throughout history, Rolex have developed a strong reputation for genuine innovation within the field of watch-making. In total, the company has registered more than 400 patents and its list of innovations includes creating the first ever waterproof wristwatch (Oyster), creating the first watch to resist water at depths of 100 metres (Submariner) and developing the first wristwatch to display two different time zones simultaneously (GMT-Master).
Divers watches produced by the company are each tested individually, using pressurised water tanks to assess their resistance to water. It is said that less than one watch in every 1,000 fails the rigorous testing process, which is a testament to the accurate work carried out in the various Rolex facilities.
The Year-Long Production Process
Despite producing close to one million watches every single year, the production process for each watch takes around 12 months from start to finish, giving an insight into the care that is taken to make sure every single Rolex timepiece meets the standards that customers have grown to expect.
The entire Rolex production process is based around not taking short cuts, as demonstrated by the sheer amount of in-house processes. Moreover, the company is keen to ensure each part of the process is performed as accurately as possible, regardless of cost involved or the time needed.
Parts of the process which need attention to detail and the ability to spot problems are usually carried out by hand, whereas Rolex have been perfectly willing to invest in machinery for aspects which require an inhuman level of accuracy. Finally, no stone is left unturned during the extensive testing phase each timepiece goes through, and all watches leave the Swiss facilities having passed an array of checks to guarantee quality.
Most popular Rolex Models in our Shop:
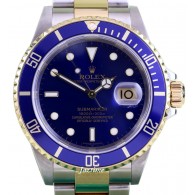
» learn more
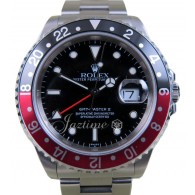
» learn more
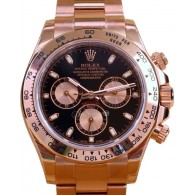
» learn more